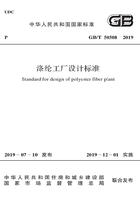
上QQ阅读APP看本书,新人免费读10天
设备和账号都新为新人
3.4 工艺计算
3.4.1 熔体输送、切片输送、结晶、干燥,纺丝及后处理工艺设备配置,应以单台(套)设备的生产能力为依据,并应结合产品方案的产量、设备运转效率,计算所需台(套)数。
3.4.2 纺丝和熔体输送设备及熔体夹套管应进行热量衡算。
3.4.3 组件清洗设备配置应根据设备清洗能力和清洗周期,以及需清洗的纺丝组件、喷丝板、计量泵、过滤芯的数量,计算所需台(套)数。
3.4.4 纺丝熔体管道应进行下列计算:
1 应通过计算保证所选熔体管道的管径分配和长度,满足生产相同产品的每个纺丝箱体熔体输送管道内的熔体压力降和熔体停留时间相等,且熔体黏度降应在纺丝允许范围内;
2 纺丝熔体管道设计应进行管道系统的热应力分析计算,在满足安全性的前提下,管道长度应最短;
3 纺丝熔体管道设计应进行管道系统熔体压力降、熔体停留时间和黏度降计算,确定优化的熔体管道内径和长度。
3.4.5 熔体直接纺丝工艺应根据熔体增压泵出口熔体温度和生产能力,计算熔体冷却器的热负荷及换热面积。
3.4.6 热媒空冷器的换热面积应根据热负荷计算确定。
3.4.7 每条纺丝生产线的热媒加热设备的能力及热媒循环量应根据工艺参数和装置生产能力计算。
3.4.8 纺丝机丝束冷却风的风量应根据产品方案中线密度上限产品的最大冷却量和工艺要求的最低冷却风温度等参数计算。
3.4.9 纺丝油剂调配系统的能力及配置应根据产品方案计算。
3.4.10 组件预热炉、运转丝车、盛丝桶、打包机等的能力应根据产品方案计算。